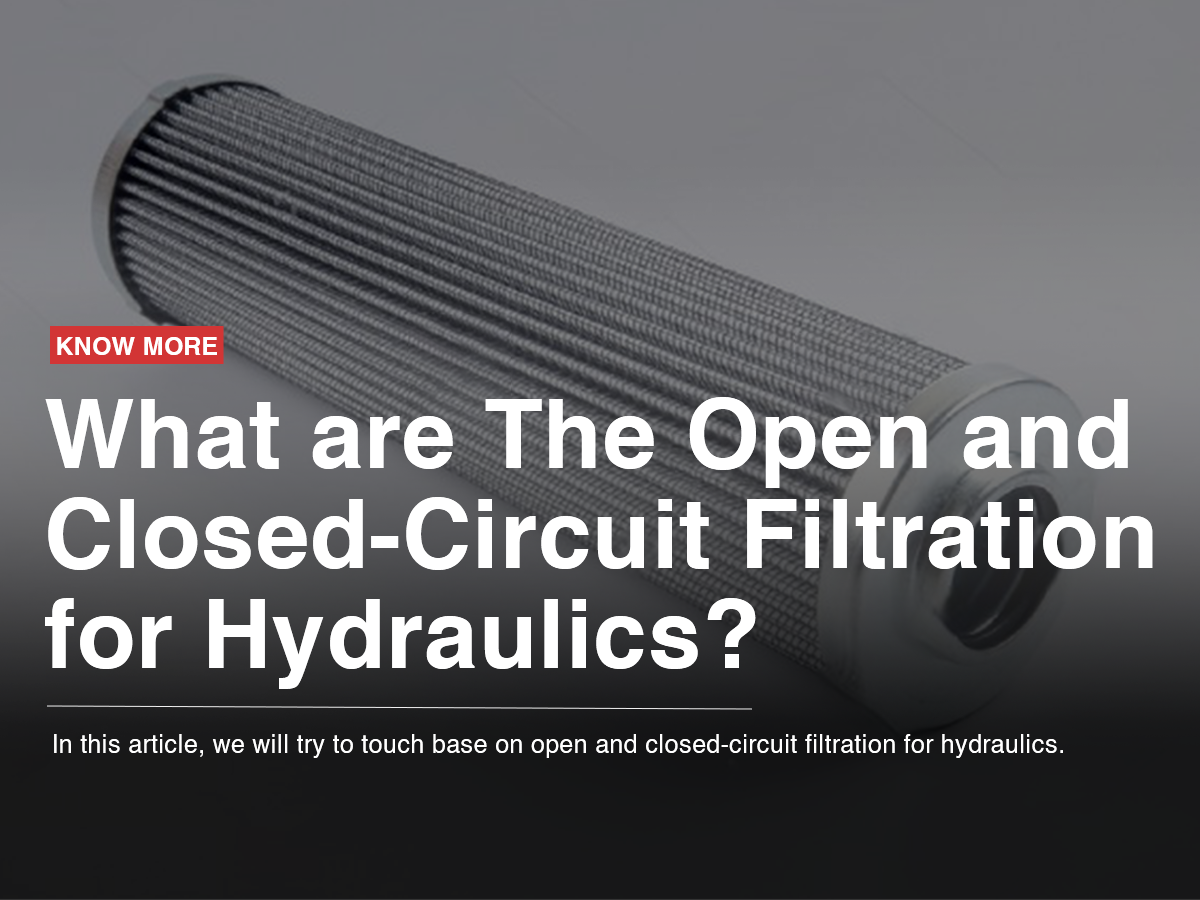
What are The Open and Closed-Circuit Filtration for Hydraulics?
This article aims to provide an overview of open and closed-circuit filtration for hydraulic systems. It is essential to note that every hydraulic system is unique, and filtration requirements and performance should be determined through testing with the manufacturer.
Selecting the right filtration system for your operation is paramount to maintaining fluid cleanliness and preventing premature wear, both of which significantly contribute to optimal system performance and service life.
Hydraulic systems are vulnerable to various contaminants that can occur during assembly and operation. Among these, dirt poses the most significant threat, but contamination can manifest in the form of water, other fluids, air, solid particles, corrosive agents, and heat. Consequently, it is crucial to ensure that only clean fluid enters the hydraulic circuit. For superior durability and quality, it is recommended to employ a filter capable of maintaining fluid cleanliness to ISO 4406 class 22/18/13 or better under standard operating conditions.
In closed-circuit designs, two essential filtration points are worth mentioning:
-
Suction Line Filtration: In this setup, a filter is placed between the fluid reservoir and the inlet of the closed-circuit pump. A vacuum gauge can be employed to monitor when the inlet pressure exceeds the manufacturer's requirements. Optimal cleanliness levels of 18/13 under normal operating conditions can be achieved by using a filter with a β35- β45 = 75 (β10 ≥2) at a differential pressure of 0.25bar. In some applications, even higher cleanliness levels may be achieved, as demonstrated in tests.
-
Charge Pressure Filtration: Placing the filter in the charge circuit helps reduce high inlet vacuum during cold start-up conditions. It provides instant fluid filtration ahead of the pump's control and the hydraulic loop. Recommended filter elements are those with a β15- β20 = 75 (β10 ≥ 10) at the differential pressure occurring in the application. Additionally, a strainer with a mesh size of 100 µm - 125 µm is essential to safeguard the charge pump against coarse contamination.
Regarding charge pressure filtration, there are two options to consider:
a. Partial Flow: Refers to the placement of the charge pressure relief valve upstream of the filtration, where only a portion of the charge pump oil flows through the filter, while the rest flows over the charge pressure relief valve back to the reservoir.
b. Full-Flow: Has the charge pressure relief valve downstream of the filter element. Here, all the charge pump flow is directed through the filter, significantly enhancing filter efficiency when compared to suction filtration.
On the other hand, in open-circuit designs, suction filtration is not recommended for open-circuit pumps. Instead, it is advisable to utilize a screen in the reservoir, covering the pump inlet. A 125 µm (150 mesh) screen effectively protects the pump from ingression of coarse particles. The preferred method for open-circuit systems is return line filtration, where the filter is positioned in the return line to the reservoir.
When choosing a return line filter system, several factors should be taken into account, including cleanliness specifications, contaminant ingression rates, flow capacity, and the desired maintenance interval. By considering these factors, hydraulic systems can maintain optimal performance and longevity.